POSITION TITLE - DEPARTMENT - LOCATION
POSITION DESCRIPTION
Your content goes here. Edit or remove this text inline or in the module Content settings. You can also style every aspect of this content in the module Design settings and even apply custom CSS to this text in the module Advanced settings.
POSITION DETAILS
Work Type: Full Time
Location: Location
Categories: Departments
Applications Close: Ongoing / Closed
KEY REPONSIBILITIES
Develop and execute project health, safety, environmental and quality plans. Including developing JSA/SWI and undertaking project risk assessments, conducting pre-start up meetings
Provide relevant WHSEQ information to site personnel
Understand and meet project demands
Provide high level customer service
Provide strong leadership to the construction team
Manage day to day operational aspects of the project
Analyse and forecast project profitability, revenue, margins, rates and utilisation
Set and manage client expectations
Develop lasting relationships with client personnel that foster client ties
Identify value adding opportunities as they relate to a specific project
Leading a project as well as leading a team for the design process
Develop and execute project health, safety, environmental and quality plans. Including developing JSA/SWI and undertaking project risk assessments, conducting pre-start up meetings
MINIMUM QUALIFICATIONS & REQUIREMENTS
Degree qualified – Structural / Civil or Mechanical Engineering
Strong experience in the food and beverage construction industry
Minimum five years project management experience
Excellent English communication skills (verbal and written)
General understanding of regulatory requirements for electrical and safety systems
To be successful in this role, you must possess strong organisational, planning, verbal and written communication skills. You must also have the ability to follow directions and demonstrate innovative problem solving as an individual and as part of the team.
The ability to work away may be required in this position
A competitive salary will be offered to reflect experience and skill
This position is open only to those eligible to work in Australia
Applicants must be able to comply with police check and drug testing requirements.
HOW TO APPLY
Please click on the link below and send us your resume and all applicable supporting documents with the position referenced in the subject of the email.
Explore More
Learn more about our company and its capability to undertake major demolition, decommissioning and deconstruction projects.
News & Media
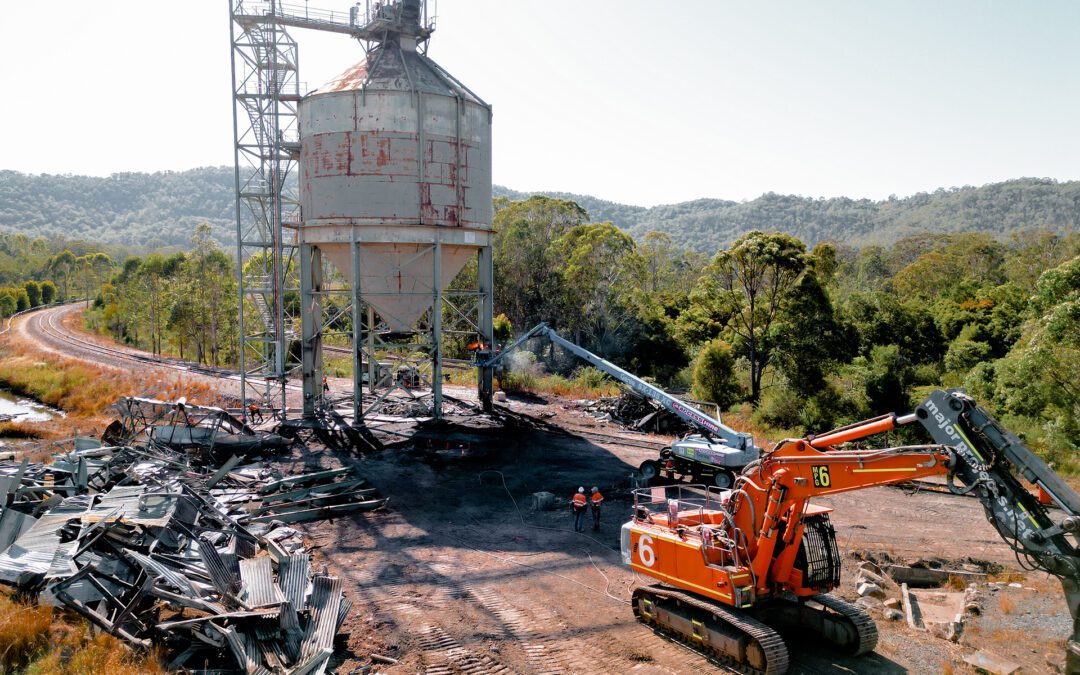
Guide to coal plant demolition
Sep 15, 2023
Guide to coal plant demolition
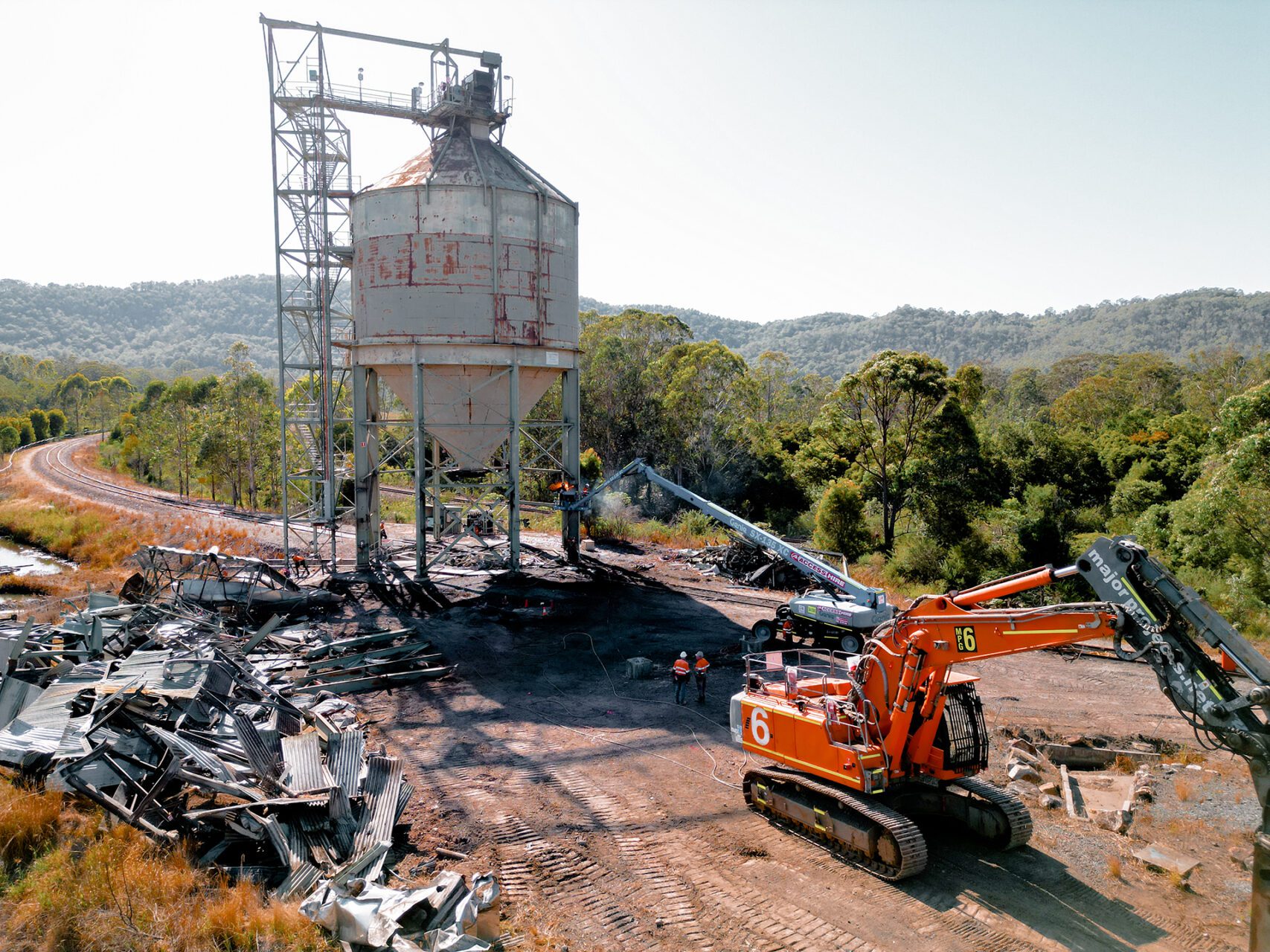
Several factors are fueling coal plant demolition in Australia and across the globe. With the shift towards renewable energy resources, recent caps on greenhouse gas emissions, and extra wastewater regulations to consider, an increasing number of coal-fired operations are proving non-viable.
But how can you demolish a coal plant efficiently, recover valuable scrap metal and preserve the land for redevelopment?
To achieve these goals, the demolition of a coal plant must be approached with extreme diligence and care. This complex process involves multiple stages, from decommissioning, safety assessments and hazardous material abatement to dismantling, waste removal and site remediation.
It’s vital that plant owners understand the strategies, documents and risks of each of these milestones. That way, it is possible to protect the plant’s workers, community, surrounding environment and reputation.
Below, we explain the core steps to successful coal plant demolition. Keep reading to discover the key preparation and administrative duties of plant owners and demolition contractors throughout this high-stake project.
Coal plant decommissioning
The first step is to decommission the coal plant. This involves notifying all personnel of the closure, shutting down operations and getting rid of any in-process or raw materials.
As the plant owner, you may also choose to sell certain assets, such as electrical generating equipment, on the scrap market to recoup the investment. Additionally, you can also sell the land to a property developer or other organisation at this stage for redevelopment.
Assessments and planning
The next step is to examine the structures to be demolished and the land on which they stand. Performing in-depth risk assessments is crucial to flagging and mitigating all potential hazards before coal plant demolition takes place.
As well as protecting the community and informing the demolition plan, these reviews will help to ensure your project abides by environmental legislation and national safety standards.
Pre-demolition assessments typically include:
- A site survey to analyse environmental risks and confirm the scope of work required.
- An engineering assessment to determine structural integrity, design and relevant building codes. These insights will help to pinpoint the most appropriate method of coal plant demolition.
- An electrical assessment to clarify the power supply across the site, as well as any isolation needs.
- A fire assessment to check for flammable materials and confirm the fire prevention and control measures required throughout decontamination and demolition.
- A work health and safety assessment to identify potential dangers to personnel and develop suitable protective and emergency protocols.
- A hazardous material (HAZMAT) inspection to verify the nature and location of hazardous materials, such as asbestos.
Equipped with the above findings, your contractor will prepare a detailed demolition plan that covers all key project details, including the:
- Location of the target structure;
- Any structural support systems;
- Distances between this structure and nearby buildings, infrastructure and public spaces;
- Method of demolition and the series of tasks to be performed; and
- Project timeline and estimated completion date.
It is also important to implement other plans, such as a Health & Safety Management Plan, Waste Management Plan and Environmental Management Plan. These strategies should detail the procedures needed to carry out your project in line with relevant legislation and the demolition contractor’s integrated HSEQ management system.
Mach Energy Conveyor Demolition
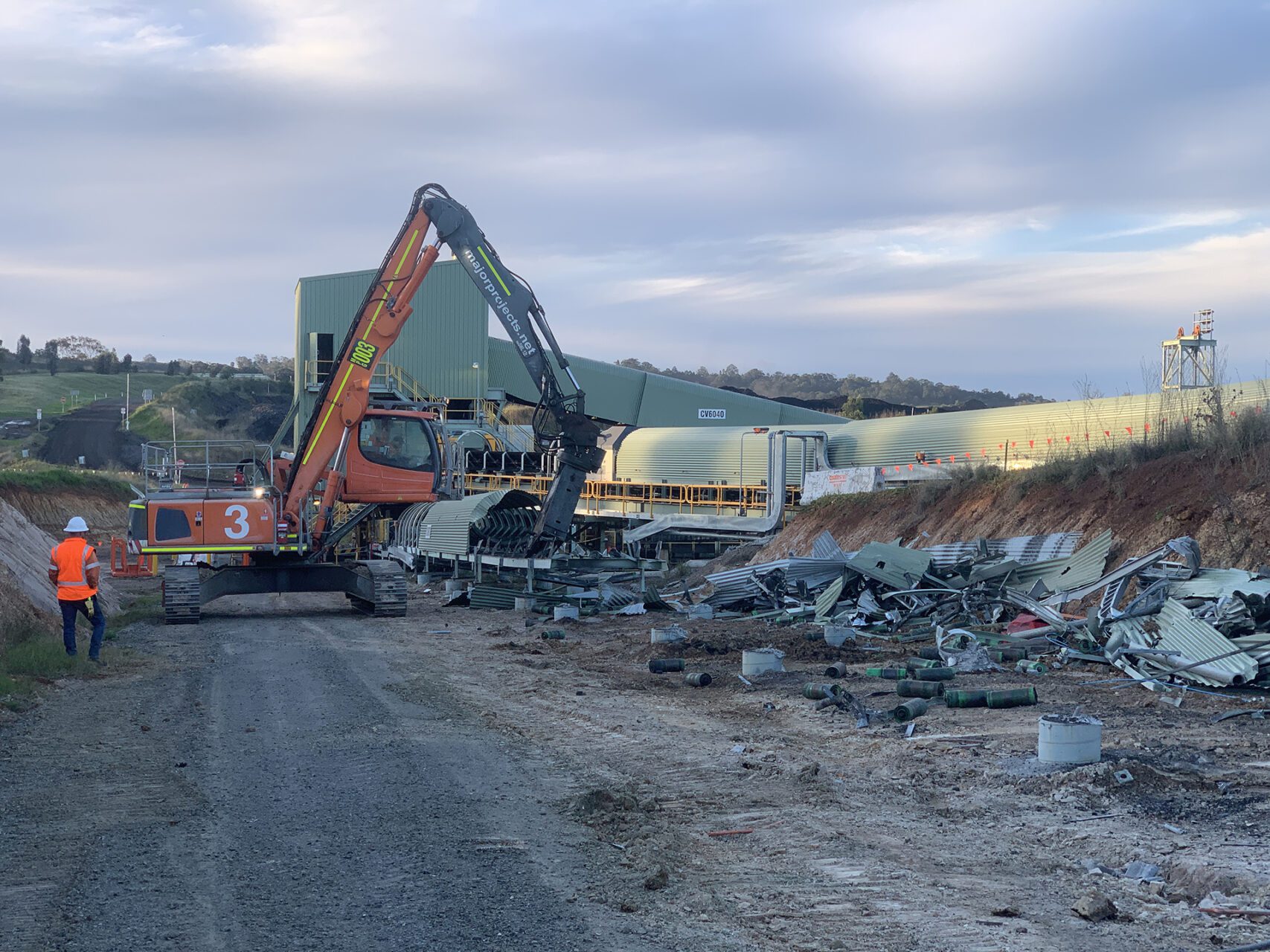
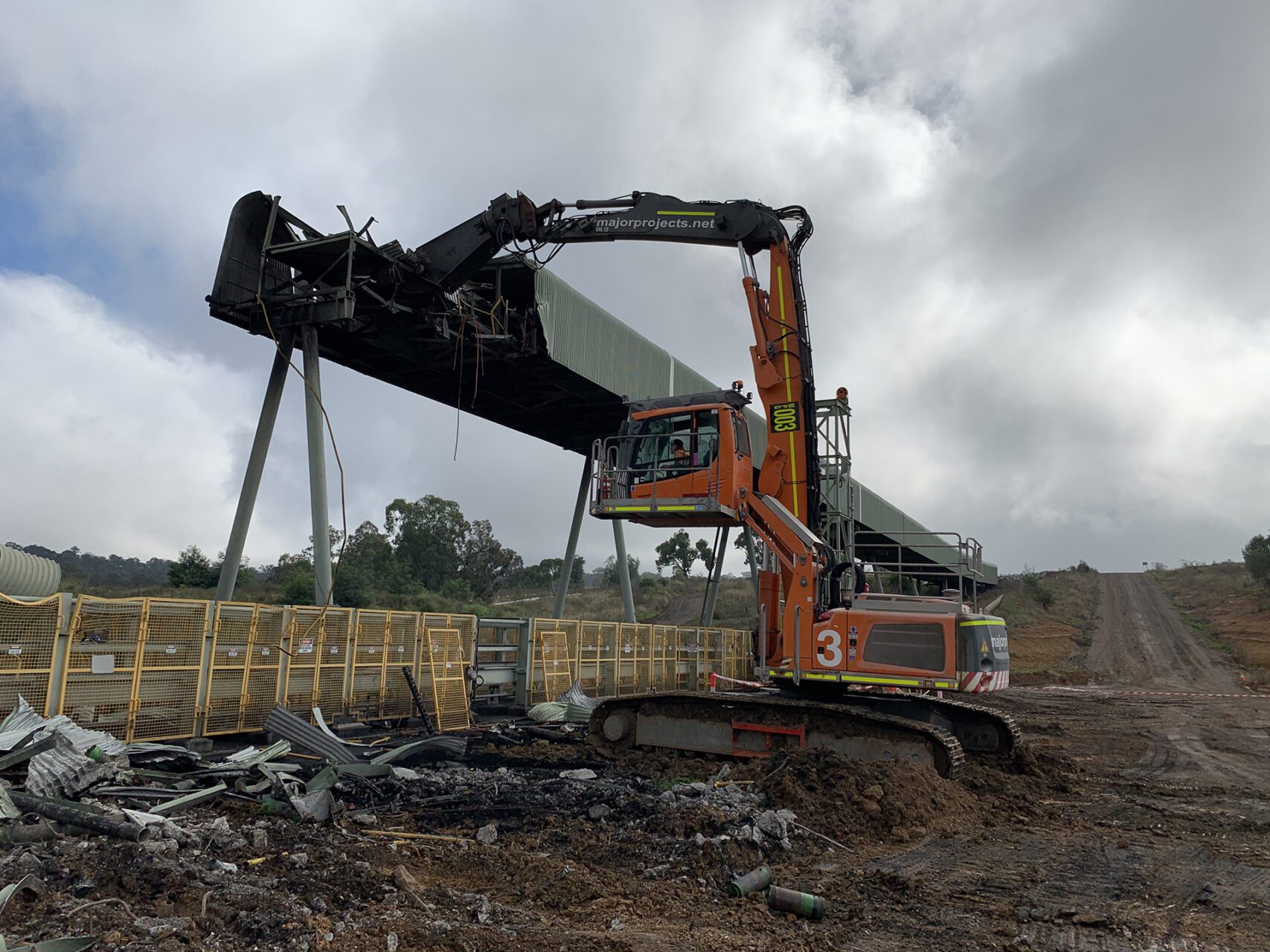
Hazardous abatement and remediation
Moreover, if the site is intended for redevelopment after demolition, it must be free from harmful contaminants and therefore qualify for a Clearance Certificate – which is necessary for any construction down the line.
Therefore, it’s important to budget for hazardous material assessment and removal services, as well as add an appropriate buffer in the overall project timeline.
With a Class A (Friable) Asbestos Licence in the majority of Australian states and territories, Major Projects Group draws on over 40 years of industry experience to provide unparalleled asbestos and hazard material removal services for coal plant demolitions.
We partner with expert subcontractors to utilise state-of-the-art resources that maximise efficiency. Our end-to-end solutions include inspections, testing, air monitoring, abatement, encapsulation, disposal, waste management, consulting and more.
Yancoal Stratford and Duralie CHPP Demolition
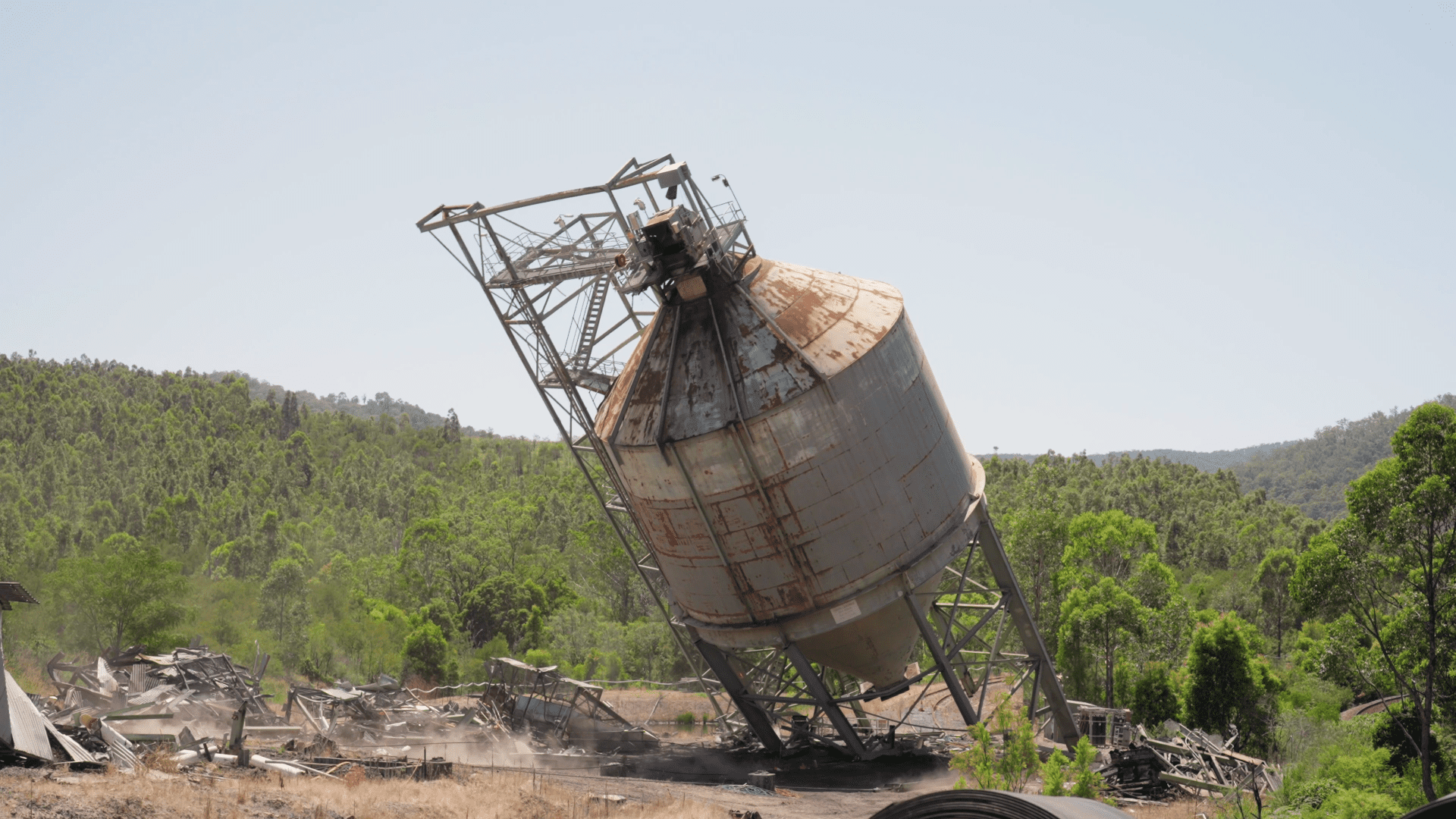
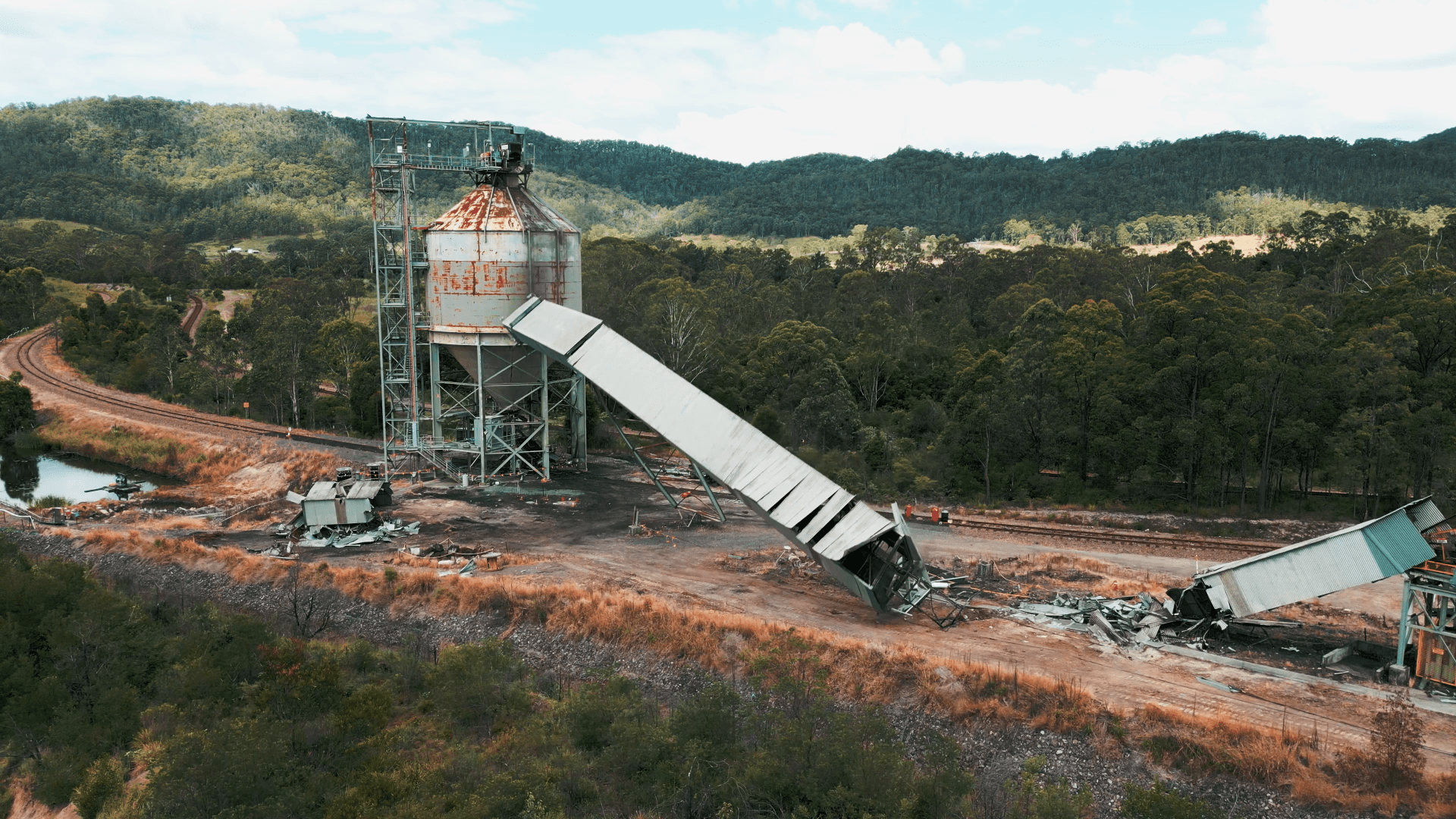
Coal plant demolition
Each structure is demolished using explosive, mechanical, induced collapse and/or high-reach methods, depending on its construction, contents and clearance. Whatever techniques are used, the demolition will be completed in a controlled sequence of steps, between which another round of decontamination may be performed as required.
Throughout this process, your contractor will monitor and log every task, risk, protocol and outcome for your review. This includes all information that a plant owner, and any subsequent site owners, may need in the future, including what structures were demolished, where and how they were disposed of, which assets were scrapped and sold, what site remediation efforts took place and more.
A critical deliverable for every coal plant demolition, this meticulous documentation ensures that you have a complete record of the project after its completion.
Discover more about the general demolition process with Major Projects Group.
Site remediation and waste removal
Site remediation refers to the assessment and removal of hazardous materials after coal plant demolition. As the site owner, it is your responsibility to ensure this cleanup satisfies all regulations.
First, soil and groundwater samples should be examined for contamination. If your coal plant is beside a body of water that has been contaminated by its operations, this must be addressed as well. You will then need to devise and action an effective cleanup plan based on the investigation’s findings.
Remediation also includes determining the site’s requirements for redevelopment. Coal plants are usually situated near integral infrastructure, with easy access to transport networks, water, and fibre connection. Often, these advantages make the land highly attractive for commercial, industrial, residential and even community-focused projects, such as public parks.
With myriad technicalities to take into account, it is essential that you partner with a coal plant demolition contractor who understands how to dispose of all waste and detritus safely in accordance with the site’s next intended use.
If it is to be a greenfield site, you must replace the top several layers of dirt with fresh fill dirt, clean topsoil, seed and straw to restore it to the condition it was in before the coal plant’s construction.
Alternatively, if the property is going to be a brownfield site, then you may only be required to remediate contaminated zones. For instance, if the land will be used for housing, cleanup requirements may be more strict than if a factory were to be built, as there is less risk of direct or extended exposure to contaminants.
At Major Projects Group, we possess the specialist knowledge, permits and licences to take care of waste removal and site remediation after coal plant demolition. We can guide you through any course of action, including:
- Completely removing dismantled or demolished parts;
- Scrapping certain dismantled or demolished parts and salvaging the rest for other applications; or
- Moving dismantled or demolished parts to a new location.
A word on stakeholder management
It’s important to understand that coal plant demolition will have a significant effect on a variety of key stakeholders, from workers, neighbours and business partners to environmental organisations, government authorities and industry bodies.
Transparent, sensible and considerate consultation with these groups from the outset can help to streamline the entire process moving forward. That’s because a shared vision and open dialogue reduce the risk of future objections and other obstacles, which could otherwise delay the demolition or waste resources.
With engaged and motivated team members helping to facilitate the closure from start to finish, you will ultimately achieve a more efficient outcome.
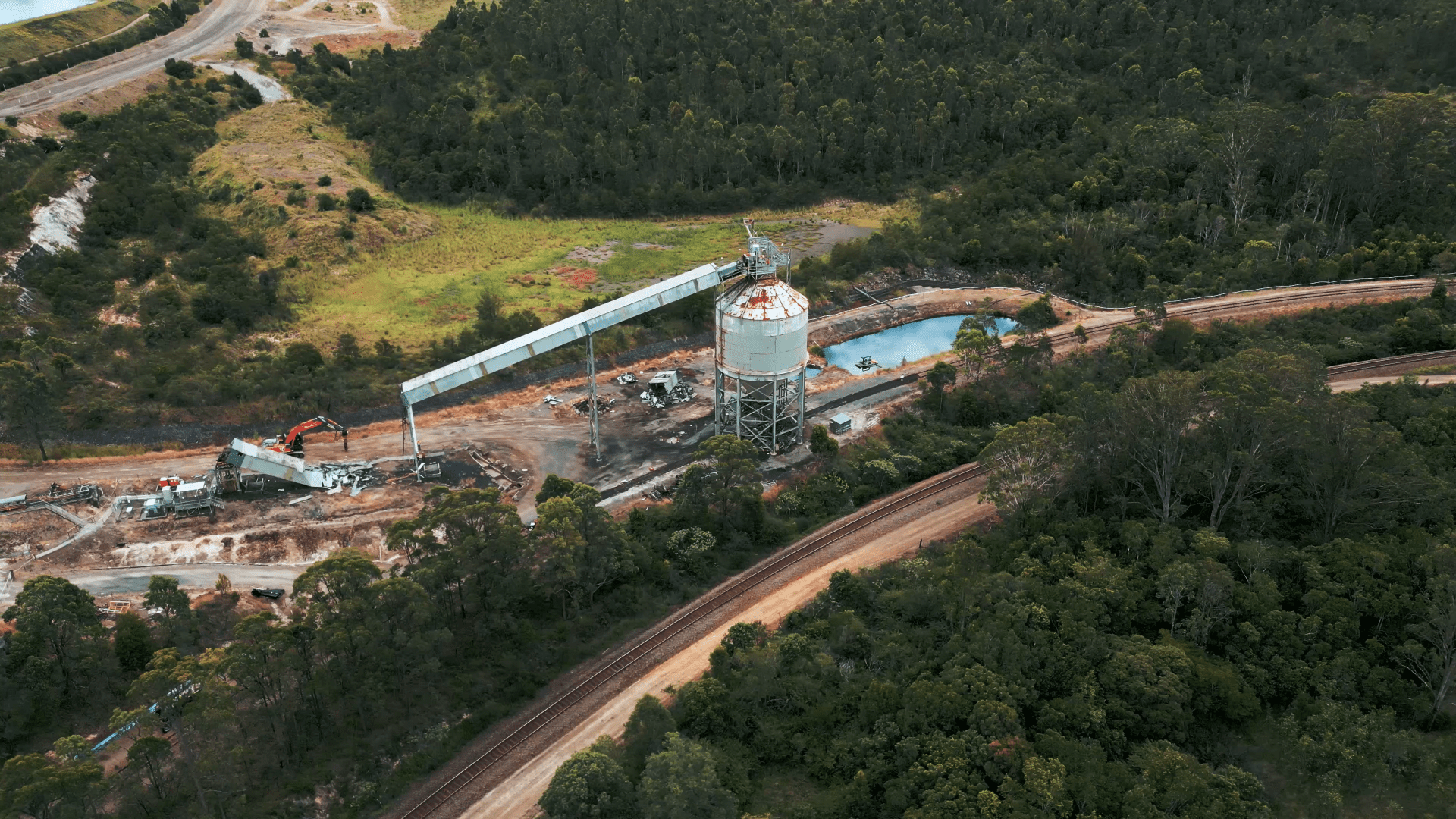
Demolish your coal plant with Major Projects Group
Major Projects Group is proud to be a Social Enterprise leading environmental stewardship in the demolition industry. Our expert team leverages the latest equipment and certified HSEQ management systems to take care of coal plant demolitions throughout Australia.
We provide a complete range of capabilities, including decommissioning, dismantling, demolition, asset recovery and asbestos and hazardous material removal – all of which are performed with minimal impact on the surrounding people and environment.
To start your coal plant demolition with Major Projects Group, please enquire today at +61(0)2-4967-7900 or [email protected]
News & Media
Contact Us

Newcastle Head Office
121 Woodstock Street
Mayfield, NSW 2304
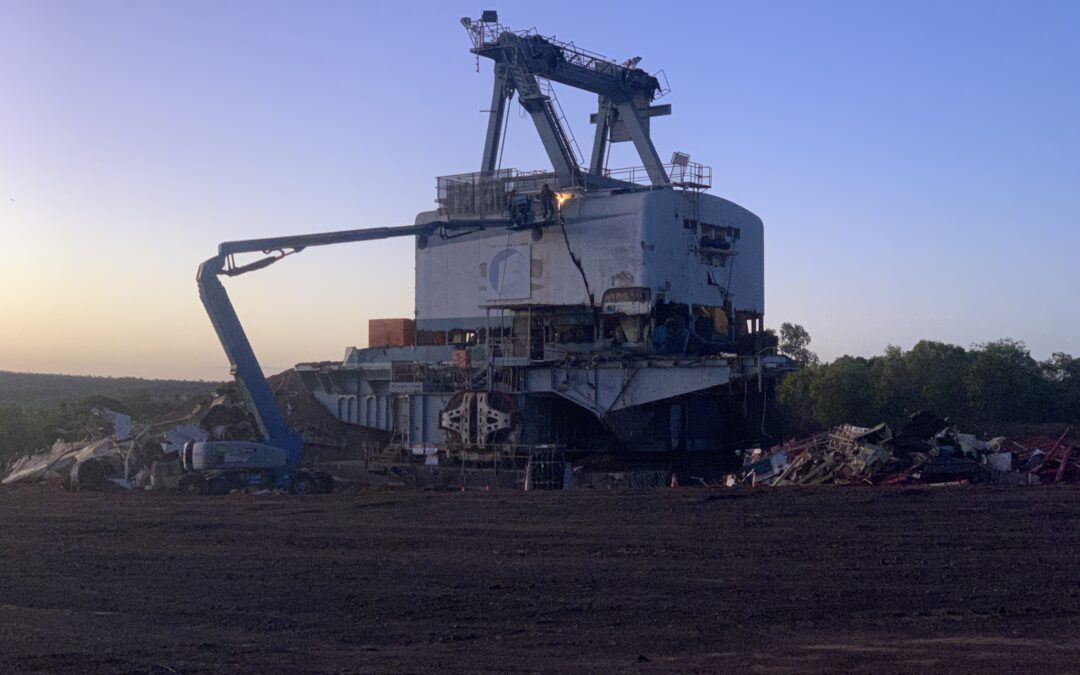
Dragline mining & demolition explained
Sep 6, 2023
Dragline mining & demolition explained

Draglines are heavy-duty excavating tools used to remove overburden in open-cut mines across Australia. While this huge piece of machinery can be highly productive and cost-effective, it will not remain feasible forever. Eventually, an abandoned or decades-old dragline will need to be demolished and removed from the mine site.
Below, we explain how mine draglines work, including information on their methods, components, and demolition. Read on to discover more about dragline mining.
What is a dragline in mining?
A dragline is a mechanical excavator and crawler used during large-scale works. One of the biggest machines ever built, a dragline tends to weigh approximately 8,000 to 13,000 tonnes.
Smaller models are essentially composed of a winch drum on a lifting crane. Built offsite, they are generally used for civil engineering works, such as foundation, road and port construction, and can be easily dismantled.
Larger draglines are reserved for oil sands or coal surface mining. Assembled onsite, they stay in place for decades until demolition is required.
In mining, draglines get rid of overburden or, in other words, any material that is standing in the way of the target resource. For instance, removing the surface soil and rock above a coal seam. This overburden can then be stored and used to refill the open pit once mining operations cease.
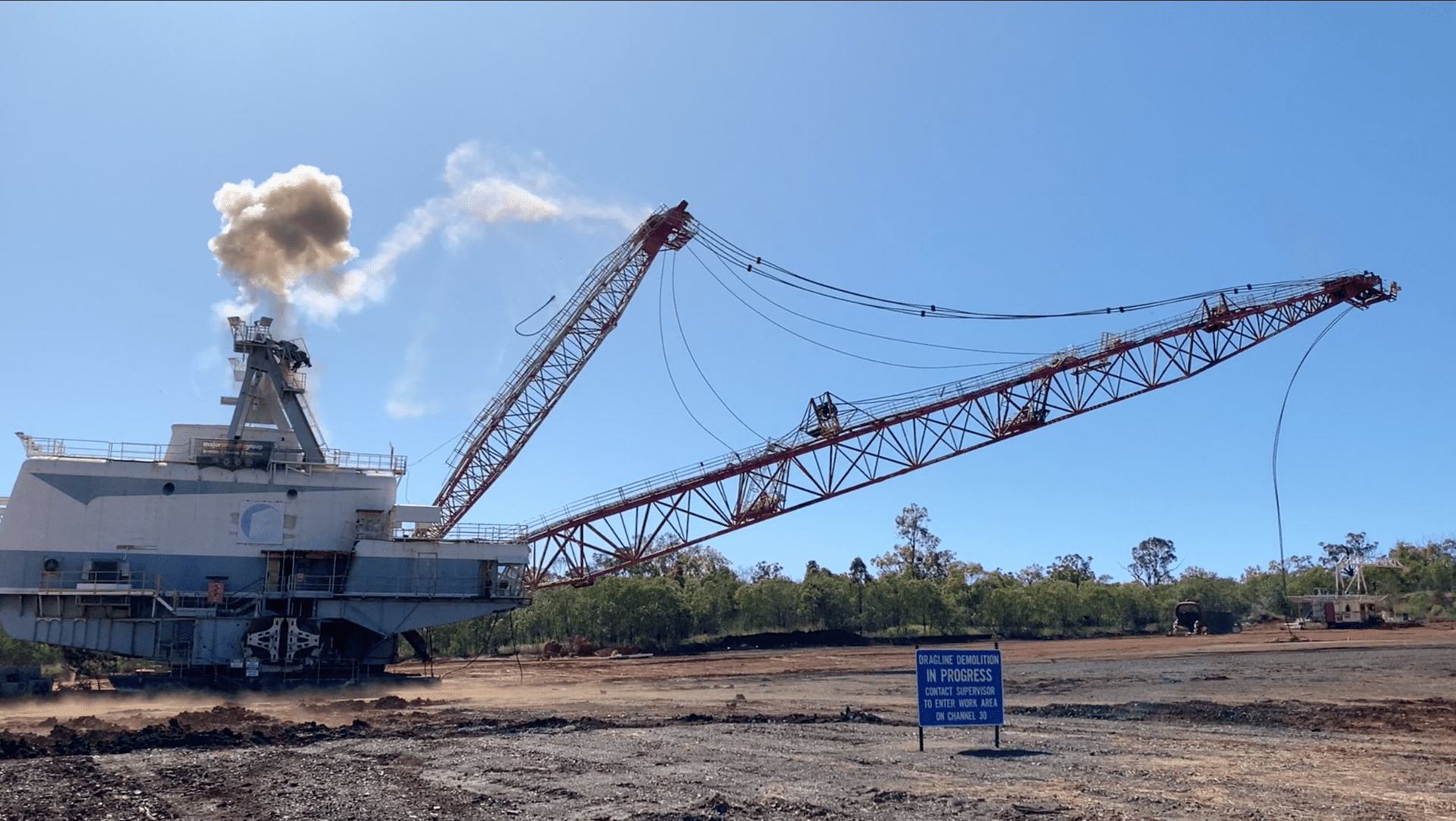
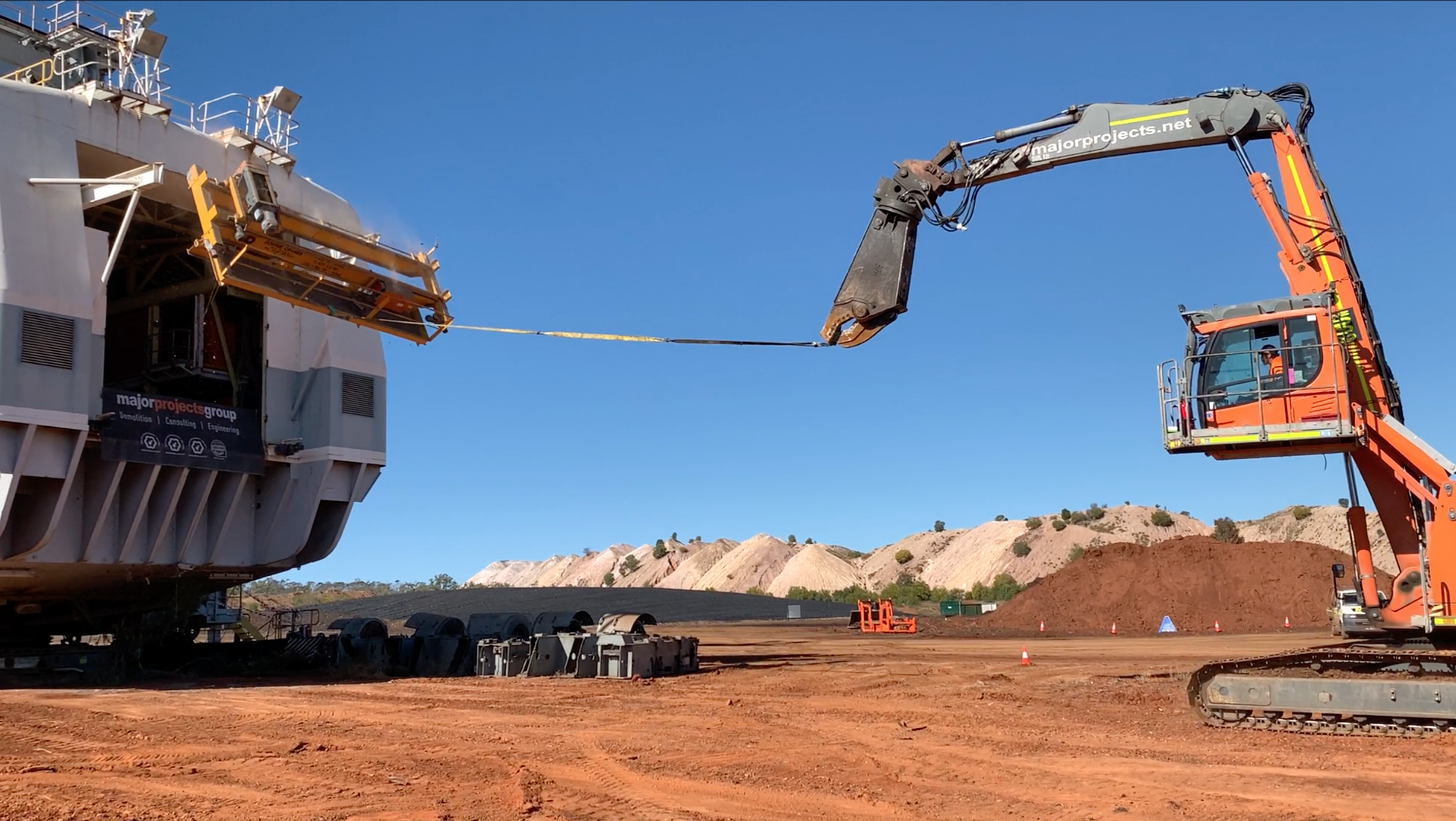
How do mining draglines work?
A mining dragline dismantles and moves overburden in a similar way to a crane. A massive bucket is cast out from the machine’s body and then pulled inwards, shovelling material along the way.
Multiple ropes are used to adjust this process, which enables your team to scoop up and dump material nearby in far less time than with a standard excavator.
Importantly, precise dragline mining methods depend on the size and model, which can offer various levels of drag, rotation and displacement.
Unlike the majority of machinery in mines, most draglines do not run on diesel. Instead, they are powered directly via the high-voltage grid, at voltages varying from 6.6 to 22kV. A typical dragline consumes up to 6 MW during standard mining operations.
5 key dragline components
1. Machine body
The machine body is the core structure upon which other components are assembled. It houses the dragline’s engines and operator’s cabin. Depending on its design, this body can feature continuous tracks or be placed on pontoons.
2. Boom
The boom is a metal structure that extends from the machine body. The hoist rope that holds the bucket hangs from this truss-like structure.
3. Bucket
The bucket is a toothed shovel or scoop that excavates, loads, transports and unloads overburden at the intended location. Depending on the dragline’s size, the mine site conditions, and the overburden’s properties, different techniques can be used to operate the bucket. However, this component can generally move up and down via the lifting cable or forward and backward via the drag wire.
4. Hoist rope
Also known as the lifting cable, this motor-driven rope hangs from the top of the boom. It holds the bucket away from the boom and is used to raise or lower it – all while supporting the hoist-coupler assembly.
5. Drag rope
The drag rope connects the machine body to the bucket. It can extend or retract to bring the bucket forward or backward, respectively, as well as adjust its inclination as required, in line with the lifting cable’s movements.
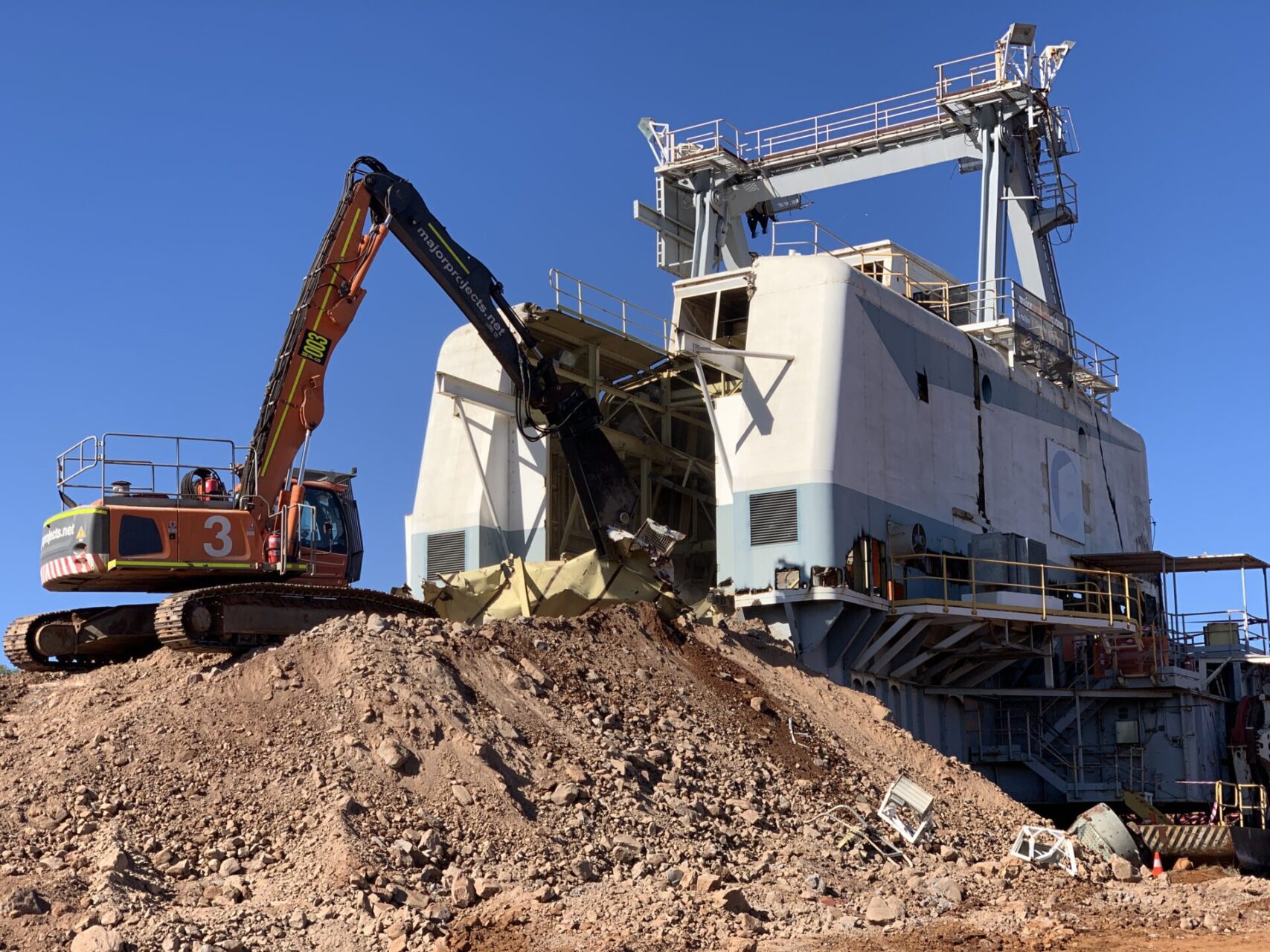
Mine dragline maintenance and shutdowns
When it’s time to service a dragline, you will need to implement a scheduled mining shutdown. Dragline maintenance can take anywhere from 4 to 12 weeks depending on its scope, and may be required several times a year.
This procedure involves work inside the confined space of the machine, with support and other tasks provided by spotters outside. Therefore, effective communication and strict Work Health and Safety protocols are both essential to your team’s safety.
Additionally, in some cases, it may be more cost-effective to dismantle or demolish an outdated mining dragline and replace it with a newer model.
The way forward for mining draglines in Australia
Compared to other mining machinery, draglines have remained relatively similar in design and operation systems. But that’s about to change. With manual operators causing up to 15% variation in product results, mining companies like CSIRO, MineWare and CRCMining are collaborating with the University of Queensland to develop automated systems that enhance efficiency.
This revolutionary technology identifies the most optimal sequence of movements for a mining dragline to excavate overburden. The aim is to provide operators with real-time guidance on position, digging and dumping, helping them to make informed decisions on dragline sequencing.
The result? A significant boost in productivity.
Mine dragline demolition
A mining dragline can be demolished with mechanical, explosive or induced collapse techniques, the most appropriate of which depends on site conditions and project requirements. If you are ready to remove and replace your old mining dragline, Major Projects Group is here to help. Our experienced dragline demolition contractors can take care of everything from decommissioning and dismantling to asset recovery and site remediation.
For example, Idemitsu recently engaged Major Projects Group as the Principal Contractor to demolish a Bucyrus Erie 1,260W dragline at the Ensham Resources mine site in Comet, Queensland. We performed 12 induced collapse demolition drops in total, recording over 3,300 man-hours and processing at least 1,300 tonnes of scrap steel – all of that with 0 safety incidents.
Explore more of our mining demolition projects.
Ensham Resources, Dragline DLO3 Demolition - Comet, QLD
Yancoal, CHPP Demolition & Salvage Stage 1 - Stratford & Duralie, NSW
BMA Blackwater Coal Handling
BHPB Nickel West Demolition Works
BHPB Newman Mine Rehabilitation
Xstrata Zinc Crusher
Xstrata Copper Mount Isa Cu Crusher
RGP3 Goldsworthy Finucane Island
Finucane Island Beneficiation Plant Port
Catherine Bay Coal Washery
BHPB Newcastle Steelworks
Hamersley Iron Tom Price Mine
Alcan Gove Thickeners Tanks
Xstrata Mount Isa Fsr Plant
Enquire about mine dragline demolition with Major Projects Group
Demolishing a mine dragline involves a plethora of processes, regulations and technicalities, so it is essential to engage an experienced contractor with a proven track record. Dedicated to excellence in dragline demolition, Major Projects Group has been trusted by many of Australia’s largest mining companies, including Glencore, Mach Energy Australia, Idemitsu, Rio Tinto and BHP Billiton.
As a Social Enterprise advocating environmental stewardship, we utilise the latest equipment and certified HSEQ management systems to complete even the most complex mine site demolitions.
Discover a full range of capabilities, including decommissioning, dismantling, asset recovery and asbestos and hazardous material removal – all of which are actioned via safe, compliant and cost-effective solutions.
To start your dragline demolition with Major Projects Group, please enquire today at +61(0)2-4967-7900 or [email protected].
News & Media
Contact Us

Newcastle Head Office
121 Woodstock Street
Mayfield, NSW 2304